自動車用バッテリ管理システムをテストするためのPXIソリューションの開発
電気自動車の登場は、動車業界にとってパラダイム・シフトであり、新しい駆動システム、技術、そしてテスト計画が必要とされます。車両に必要な電子部品の増加に伴い、新たなテストと検証の課題をもたらしています。
自動車業界で採用されているハイブリッドおよびプラグイン ハイブリッドで採用されるリチウム・イオン電池のバッテリー設計には、長寿命と安全性を提供するために慎重に設計された充電システムが必要です。つまり、電気自動車で取り組むべき主要な課題の一つは、バッテリー管理システム (BMS) の効果的なテストに関係していることを意味します。BMSとは、車両の推進に必要な高レベルのエネルギーを蓄えるバッテリーの状態を管理する電子機器です。
BMSのテストを支援するために、DMC Engineering & Software Services社とピカリングインターフェース社 Pickering Interfacesは協力して、バッテリ・システムをエミュレートするPXIモジュールに基づいて、大手メーカー向けにBMSテストのソリューションを提供しています。この記事では、BMSに対して、実行する必要があるいくつかのテストとその理由について説明します。また、PXIがどのように利用され、複雑な問題に対する完璧なソリューションであったのかについても説明します。
BMSの構築とテスト
リチウム・イオンのバッテリー・セルの製造プロセスには固有のばらつきが大きく、より高度で堅牢な BMS が必要です。BMSは、各セルの充電状態(SOC)をアクティブに監視してバランスを取ることにより、モジュールまたは「スタック」内のパフォーマンスが低下しているセルを補う必要があります。バッテリ・スタックの設計には、良いセルと悪いセルの無限の組み合わせがあり、さまざまな環境条件に左右されます。これらのバリエーションと使用シナリオには、効果的なバッテリー管理システムの開発と認定のためのバッテリー・パック・シミュレーションが必要です。また、実稼働環境で使用されるテストの種類にも影響を与える可能性があります。
そのため、BMSは、ハイブリッド電気自動車 (HEV)、電気自動車 (EV)、およびプラグイン電気自動車 (PHEV) の電気駆動システムの重要な部品です。 一般的なBMSは、安全性と最適なパフォーマンスを得るために、バッテリー・パックの電圧と電流の監視、個々のセルの電圧測定、セルのバランス調整ルーチン、パックの充電状態の計算、セルの温度と状態の監視、およびパック全体の保証を含む、エネルギー貯蔵システム(ESS)のすべての機能を制御します。
そのため、BMSモジュールと関連するサブモジュールは、セル・スタックからの電圧と、関連する温度、電流、および電圧センサーからの入力を読み取る必要があります。そこから、BMS は入力を処理し、論理的な決定を行ってパックのパフォーマンスと安全を制御し、さまざまなアナログ、デジタル、および通信出力を通じて入力ステータスと動作状態を報告する必要があります。
つまり、BMSのシステムを効果的にテストするには、「(1) 必要なセンサーとBMSへのバッテリ・セル・スタックへの入力を正確にシミュレートすること、(2) 入力の結果としてBMSのシステムによって生成されるデジタルおよびアナログ出力を測定、収集、処理すること」という2つの主要な機能が必要です。
BMSの検証を必要とする理由
バッテリー・スタックのBMSの性能を別々に検証する主な理由は2つあります。これには、安全性と寿命が含まれます。
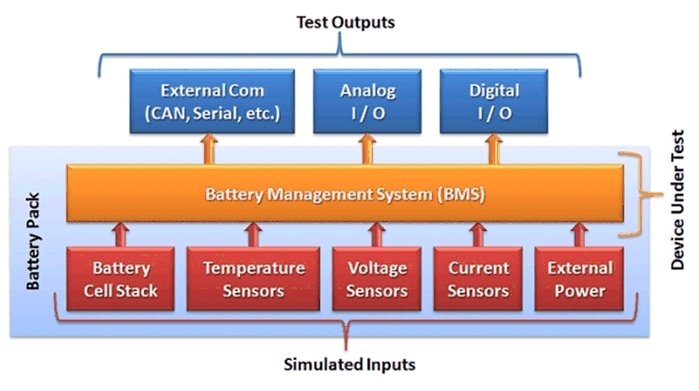
ノートPCや携帯電話のリチウムイオン電池が爆発するという恐ろしい話を誰もが耳にしたことがあるでしょう。リチウム・イオン電池の長所は、鉛蓄電池の6倍、ニッケル水素電池の3倍のエネルギー密度を持っています。さらに、適切に設計され維持されたバッテリー・スタックにより、より多くの充電/放電サイクルが可能です。 しかしながら、より多くのエネルギーを小さなスペースに詰め込み、使いやすさを向上させた事が、結果として、安全性に対する懸念を高める可能性をもたらしています。
バッテリーのエネルギーの制御された放出により、電流と電圧の形で電力が供給されますが、このエネルギーが制御されずに放出されると、有毒物質(煙など)、火災、高圧事象(爆発など)、またはそれらの組み合わせが発生する可能性があります。すべてのリチウム・イオン電池のシステムは、可燃性で「熱暴走」する傾向のある電解質を使用しています。この物質を加熱すると、自己発熱が始まる温度に達し、これにより発火と爆発に至ります。
制御されていないエネルギー放出は、機械的な安全システムと適切な物理設計によって軽減できる、押しつぶす、穴をあける、火傷などの深刻な身体的虐待によって引き起こされる可能性があります。ただし、セルの短絡、異常に高い放電率、過度の熱の蓄積、過充電、または絶え間ない再充電が原因で、バッテリーが劣化する可能性もあります。これらの原因は、バッテリー管理システムとしてよく知られている、適切に設計および検証された電子安全および監視システムによって最もよく防止されます。
BMS は、バッテリ パックの正確な充電状態を追跡する役割も担います。これは、使用可能な寿命を維持するために重要です。パックを充電しすぎたり、深く放電したりするだけで、使用可能なバッテリー寿命が劇的に短くなる可能性があります。したがって、BMS には非常に正確な電荷推定器が含まれている必要があります。バッテリーの充電を直接測定することはできないため、充電状態のパーセンテージは、電圧、温度、電流、およびその他の独自の (メーカーによって異なる) パラメータなどの測定された特性から計算する必要があります。BMS は、これらの測定と計算を担当するシステムです。BMS の充電状態の計算の精度を検証することは、パックのパフォーマンスと寿命にとって重要です。
バッテリ・スタックのエミュレーション
リン酸鉄リチウムのカソードとグラファイトのアノードを備えたリチウム・イオン・バッテリーの公称開回路電圧は3.2Vで、標準充電電圧は3.6V です。グラファイトのアノードを備えたリチウム・ニッケル・マンガン・コバルト(NMC)酸化物のカソードの公称電圧は3.7Vで、最大充電で4.2Vです。 自動車用の典型的なバッテリ スタックには、350Vを超える電圧を生成できるように直列で96個のセルがあります。 実際のバッテリー・スタックで新しいBMSシステムをテストおよび検証することは、実用的なソリューションではありません。高電圧では、低電圧システムの場合よりも細いワイヤと低損失でエネルギーを駆動システムに転送できますが、電子システムへの損傷を回避するには、高電圧を慎重に管理する必要があります。また、試験の従事者を傷つける可能性もあります。テストを繰り返し実行することはできません。そのため、BMSの信頼性が高い場合にのみ、BMSを実際のバッテリー・スタックに接続できます。 2つ目の問題は、BMSが処理するように設計されている条件をシミュレートするために、実際のバッテリ・スタック・セルの障害と特性を変更できないことです。ハードウェアとファームウェアの設計を正しく検証するには、特に開発と新製品の導入で障害を挿入することが重要です。
DMC社は、ピカリングインターフェース社に、BMSの設計を検証する目的で低電力バッテリ・スタックをシミュレートするために使用できるバッテリ・シミュレータを要求しました。バッテリ・スタックは、各セルの出力電圧を完全にプログラム可能である必要があり、スタックは電流のソースと電流のシンク(充電状態)の両方に対応できる必要がありました。
バッテリ・シミュレータの設計上の課題
ピカリングインターフェース社には、モバイル・アプリケーション向けの単一セルのPXIベースのバッテリ・シミュレータの設計経験がありました。そのため、問い合わせに続いて、設計の実現可能性調査が行われました。システムをコンパクトで低コストに保つには、できるだけ多くのチャネルを1つのモジュールに搭載する必要があると判断しました。これにより、自動車業界が正当化できる価格でコンパクトなフットプリントが実現しました。
PXIは、高密度、マルチセル、バッテリ シミュレータを設計するための理想的なプラットフォームではありません。不可能ではありませんが、モジュラーの形式によって一部の仕様が制限されました。しかし、このテストに対応するためのPXIの他のすべてのモジュールが利用可能であり、PXI が広く受け入れられていることから、PXIソリューションに焦点を当てる必要があることがわかりました。
最終製品は信頼性が高く、コンパクトで安全に使用できるものである事必用でした。PXIシャーシは通常、最大 18個のPXI周辺機器スロットをサポートできるため、設計をコンパクトにするためには、単一スロット幅のモジュールごとに、6つのバッテリ・スタックのセルをシミュレートする必要がありました。96 セル スタックをシミュレートするには、シャーシ内に 16 個のモジュールが必要です。 . この密度は、各セルの設計にいくつかのスペース制限を課します。この要件は、エンド ユーザーのプロジェクトの期限に合わせるための緊急の計画であったため、ほとんどの部品は既製品で入手できる必要がありました。
各セルは最大300mA を供給でき、各セルで4.2Vを超える電圧を生成する必要がありました。これは、シャーシのバックプレーンが各スロットとシステム全体に十分な電力を供給するための大きな課題でした。また、バッテリーをシミュレートするための高速過渡応答も必要とされている事も覚えておいてください。
PXIのバックプレーンは、5V電源で各モジュールに最大6Aを供給できます。これは、PXIのバックプレーン電源の中で最も能力が高いものです。ただし、5VからのDC変換は効率が悪いことで知られているため、設計ではかなりの損失が予想され、これらの損失がシャーシの熱負荷を及ぼしました。この問題の解決策は、+5V電源から主なセルの電力を取得し、さらに、+12Vおよび-12V電源からの電力で補うことでした。
バッテリ シミュレータの各セルは、固定の絶縁型 DC/DC コンバータを使用して絶縁型電源を提供します。絶縁型電源は、高速動作のリニア レギュレータによって調整されます。高速リニアレギュレータは、PXI 電源から離れたポイントでバッテリをエミュレートできるようにするために必要であり、出力の電圧レギュレーションを低下させたり、過度に大きな出力デカップリングコンデンサを使用したりする必要はありません。
リニア・レギュレータは、最悪の負荷条件下で大量の電力を削減する必要がありましたが、明らかに、モジュールの各セルはスペースが非常に制約されていたため、レギュレータを冷却するために使用できるヒートシンクの量が制限されていました。この問題の解決策は、自動車用に特別に設計された、高温に耐え、熱保護機能を内蔵し、PCBの銅面を冷却に使用するレギュレータを使用することでした。PXIシャーシの効率的な冷却システムにより、これらの銅の領域が十分に換気されることが保証されました。これは、特にアクティブ・デバイスが PXIモジュールの低い位置に配置されている場合に、この種類の用途で非常にうまく機能するPXI標準化された側面です。
安全性と絶縁性も設計上の大きな課題でした。バッテリ・スタックでは、96個のセルが直列に接続されており、各セルが公称 4.2V の出力電圧に設定されている場合、致命的な出力電圧になる可能性があります。絶縁バリアは、各セルの共通電圧の2倍以上に耐えながら、バッテリ・セルをプログラムで制御できるように設計する必要がありました。提案された設計では、デジタル・アイソレータを使用してPXIバックプレーンへの制御インターフェイスを提供し、ユーザーがケーブル・アセンブリをPXI モジュールの前面から外した場合に、システムがモジュールを停止できるようにする安全のためのインターロック・システムを定義しました。
BMSは、セルの充電をシミュレートする必要もありました。単純な電源は単方向で、電流のソースまたはシンクのいずれかであり、両方ではありません。BMSは両方の機能を備えている必要がありましたが、必要なシンク電流はソース電流よりもはるかに小さくすることができました。この問題は、電源をプリロードするプログラム可能な電流負荷を設計に統合することで解決されました。BMSが「充電」されているとき、電流負荷は電源がまだ電流を供給していることを保証します。
これらすべての課題と解決策が評価され、ピカリングインターフェース社からDMC社が設計および提供する新しい6チャネルのバッテリー・シミュレータの提案がまとめられました。設計の変更に関する意見交換と、期待されるパフォーマンスを明確にするための質問の後、完全なバッテリ・スタック・エミュレータが発注されました。
ピカリングインターフェース社の設計とテスト・システムでの実装
ピカリングインターフェース社は、設計の実装と最初のモジュールの構築を急速に進め、モデル 41-752 PXI Battery Simulator Moduleが開発されました。課題はハードウェア設計だけにとどまりませんでした。41-752
をテストして使用するには、ハードウェア設計チームと並行して作業するソフトウェア・サポート・チームのサポートが必要でした。最初にモジュール・ハードウェアをテストできるソフトウェアを作成し、次にユーザーが使用できる手動で各モジュールの各セルを制御できるソフト・フロントパネルを含むソフトウェアを作成しました。
このモジュールが十分な性能を発揮することが示されると、残りのモジュールが構築され、DMC社に出荷されました。DMC社は、エンド ユーザーに出荷するために、ソリューションをテスト・システムに統合しました。試行が成功し、設計に非常にわずかな調整が加えられた後、ユーザーはモジュールの納品を受け入れ、41-752が商業的に発売されました。
PXIをプラットフォームとして使用すると、このアプリケーションには多くの困難な課題が生じましたが、PXIで可能な設計の柔軟性と速度は、設計がいかに迅速に進行したかによって実証されました。バックプレーン電源、PCI制御バス、シャーシの換気システム、およびPCベースのソフトウェアのすべてにより、設計を急速に進めることができました。41-752 の場合、注文から最初のシステムの発送までわずか 8週間しかかかりませんでした。これは、他のハードウェア・プラットフォームでは不可能だった偉業です。
41-752 は現在市販されており、最大 7V の電圧と最大 300mA の電流に対して 6 チャネルのバッテリ エミュレーションを提供します。定格 750V の高絶縁バリアにより、多くのセルを D タイプ ユーザー コネクタに直列に配置できます。柔軟な安全インターロック システムにより、本質的に安全に使用できるシステムを接続できます。高電力モジュールをサポートするために使用されるピカリングインターフェース社の40-923 PXI シャーシは、最大 108 セルのバッテリ スタックをエミュレートするタスクを満たすために必要な電力と電流を提供できることが示されました。
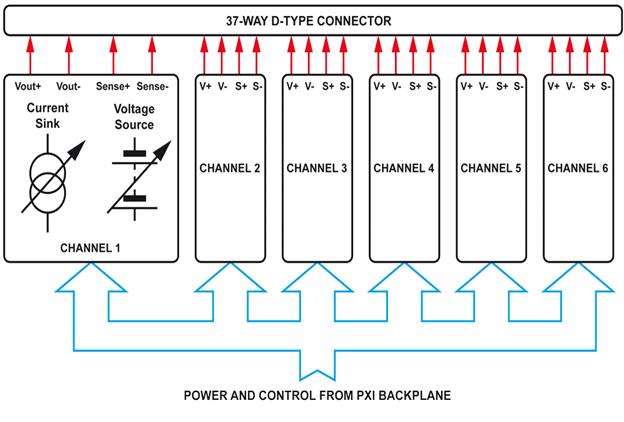
PXIバッテリシミュレータモジュール(モデル41-752)の機能図
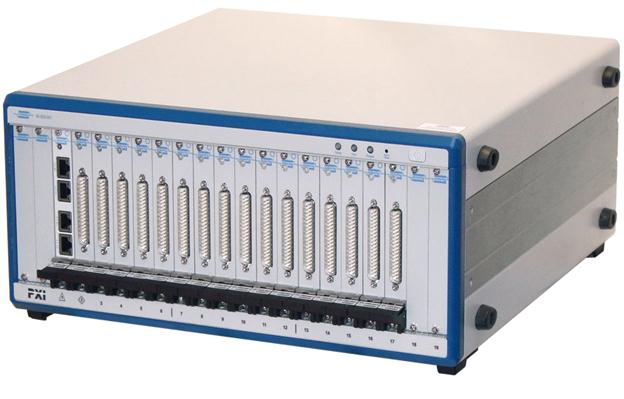
PXIシャーシ(モデル40-923)でサポートされる16枚のバッテリー・シミュレータ・モデル
PXIを使用したその他のテスト
バッテリ シミュレータに加えて、PXI モジュールは、温度センサのシミュレーション、アナログおよびデジタル I/O、バッテリ スタック出力の高電圧スイッチング、および CAN ポートを介した BMS との通信をサポートしていました。このシステムは、2 つの PXI シャーシといくつかの外部回路で構成されていました。システム全体は、奥行き 1.5 メートルのラックに収まるコンパクトなユニットであり、顧客の期待をすべて満たしていました。
結論
今後数年間で、ハイブリッドであろうと完全な電気であろうと、ますます多くの電気自動車が路上を走るようになるでしょう。長いバッテリ寿命を保証し、システムを損傷から保護するために、BMSは非常にインテリジェントなサブアセンブリになります。テストは、顧客の期待に確実に応えるために重要です。コンパクトなサイズ、コスト、および柔軟性を実現するために、PXIのテストj・システムはこれらの課題の解決に役立ちます。